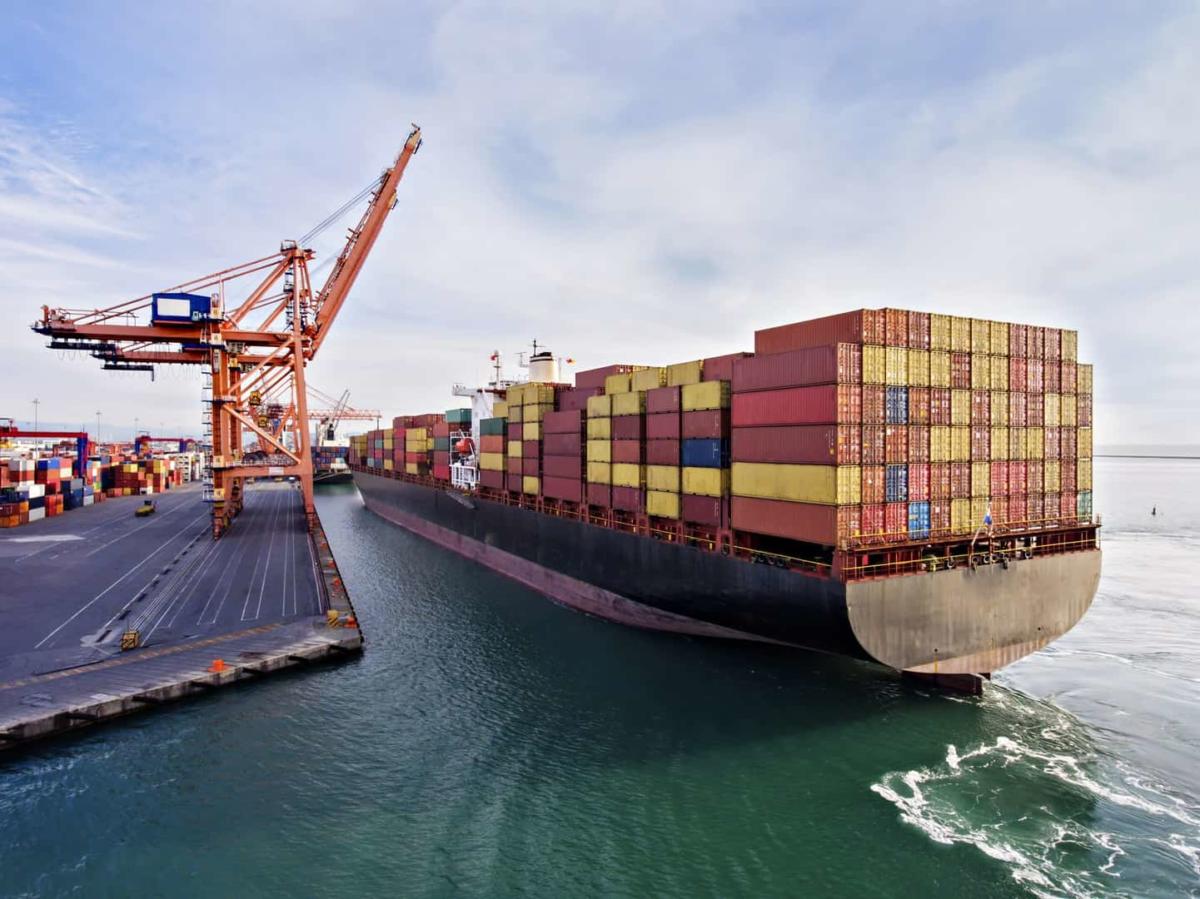
The provide chain issues brought on by the pandemic are affecting the availability of educational supplies — and this, in turn, impacts the encounter of each students and teachers. These issues are not going away any time quickly, and college district getting departments will have to come up with a strategy to assure that schools obtain supplies as they’re required.
While customer demand for goods and services continues to develop, U.S. ports and shipping providers are crippled with labor shortages and infrastructure constraints. The Wall Street Journal reports that the quantity of ships waiting to unload at the ports of Los Angeles and Long Beach, the greatest U.S. gateways for imports from Asia, is enhancing but is nevertheless hovering close to record levels. There have been 71 container ships anchored offshore on Nov. 19, WSJ reports, down from a peak of 86 3 days ahead of. Prior to the pandemic, it was uncommon for any ships to anchor offshore.
Other variables impacting the provide chain include things like higher gas rates and a shortage of truck drivers. All of these variables have place a considerable strain on college getting and supplies.
How ought to K-12 getting departments respond to these issues? Here are 4 crucial recommendations.
Adjust Buying Cycles
Purchasing of college supplies is generally accomplished in June or July to obtain supplies in time for the new college year, with the second round of purchases by early December in time for the spring semester. To get ahead of provide chain challenges, K-12 getting officers ought to look at shifting this cycle to March or April for a late summer time or early fall delivery and October or November for the delivery of spring supplies.
Stock Up on High-Volume Items Where Possible
Moving the K-12 getting cycle forward can assist assure that things are received in a timely manner and account for doable delays or back orders. However, getting departments will have to obtain lists of needed things sooner than usual. This will demand close coordination with college websites to make positive their requirements are accounted for.
For supplies that schools routinely cycle by means of immediately, K-12 getting officers ought to look at getting as a lot of of these supplies as they can afford to obtain up front, rather than waiting to acquire these things on an as-required basis all through the college year.
Stocking up on higher-volume supplies in advance can assist prevent issues with shipping delays or out-of-stock things. However, this tactic will only work if college districts have adequate money flow (or credit) to acquire things in bulk — as properly as adequate space to shop these further supplies.
Allow More Time for Large Purchases and Projects
Furnishing K-12 understanding environments is a largescale job, and it requires longer to strategy, style, provide, and set up supplies. In a common college year, arranging requires spot from November to March, which includes bidding, interviews, arranging, and style. Purchase orders generally are not issued till April or even May for summer time installations.
Because of the massive scope of these varieties of projects, we strongly recommend that you commence this procedure in early fall and challenge obtain orders in late December or January. Many makers will develop things and shop them at their facility till you are prepared for installation. Another way to prepare for summer time installations is to ship things to your district early and shop them close to the college web page. This permits the providers accountable for installation to inventory things, verify for initial harm, and order doable replacements ahead of the installation takes place.
Maintain Close Communication with Vendors
Communicating all through the getting procedure is often crucial, and that is specifically accurate in the course of uncertain occasions like these. Maintaining close communication will assist you prevent any surprises and give you time to prepare if any issues ought to happen.
Choose your vendors very carefully. Work with suppliers who are interested in forming relationships and not just closing sales. You want small business partners who are responsive to your telephone calls and emails, who will preserve you in the loop on any adjustments or new developments, and who will work with you to style inventive options when issues arise.
By arranging ahead, becoming ready, and deciding upon their vendors very carefully, K-12 college systems can prevent provide chain challenges and assure that they have the supplies they want, when they want these things — so there is no disruption to teaching and understanding.
School Specialty can assist you strategy, prepare, and execute your getting vision. To understand more, get in touch with your School Specialty representative.
Watch On-Demand
Getting ahead of provide chain challenges.
In the companion webinar, Dr. Sue Ann Highland explores the provide chain issues brought on by the pandemic and how they are impacting the availability of educational supplies. Importantly, she delivers 4 sensible approaches that can assist you lessen these impacts.
Dr. Sue Ann Highland
Sue Ann Highland, Ph.D., is the National Education Strategist for School Specialty. She has more than 25 years of encounter as an educator, administrator, and consultant with college systems across the United States.
Read more by Dr. Sue Ann Highland–>